Recognizing Welding WPS: Comprehensive Guide for Welders
Recognizing Welding WPS: Comprehensive Guide for Welders
Blog Article
Getting Welding Quality: Revealing the Secrets of WPS Implementation and Optimization
In the realm of welding, attaining quality is a quest that rests on the meticulous implementation and optimization of Welding Treatment Requirements (WPS) These fundamental records act as the foundation of welding procedures, determining the procedures and criteria essential for generating top notch welds consistently. Nonetheless, the tricks to opening the complete potential of WPS exist not just in recognizing its relevance but additionally in understanding the complexities of its application and optimization. By diving into the crucial elements, approaches, obstacles, and finest methods connected with WPS, a globe of welding excellence awaits those who want to discover its depths.
Importance of WPS in Welding
The Importance of Welding Treatment Requirements (WPS) in the welding market can not be overemphasized, acting as the foundation for making certain consistency, high quality, and security in welding operations. A WPS gives comprehensive directions on how welding is to be executed, consisting of crucial variables such as materials, welding procedures, joint layout, filler steels, interpass and preheat temperatures, welding currents, voltages, travel rates, and much more. By sticking to a distinct WPS, welders can keep uniformity in their job, leading to constant weld top quality across different projects.
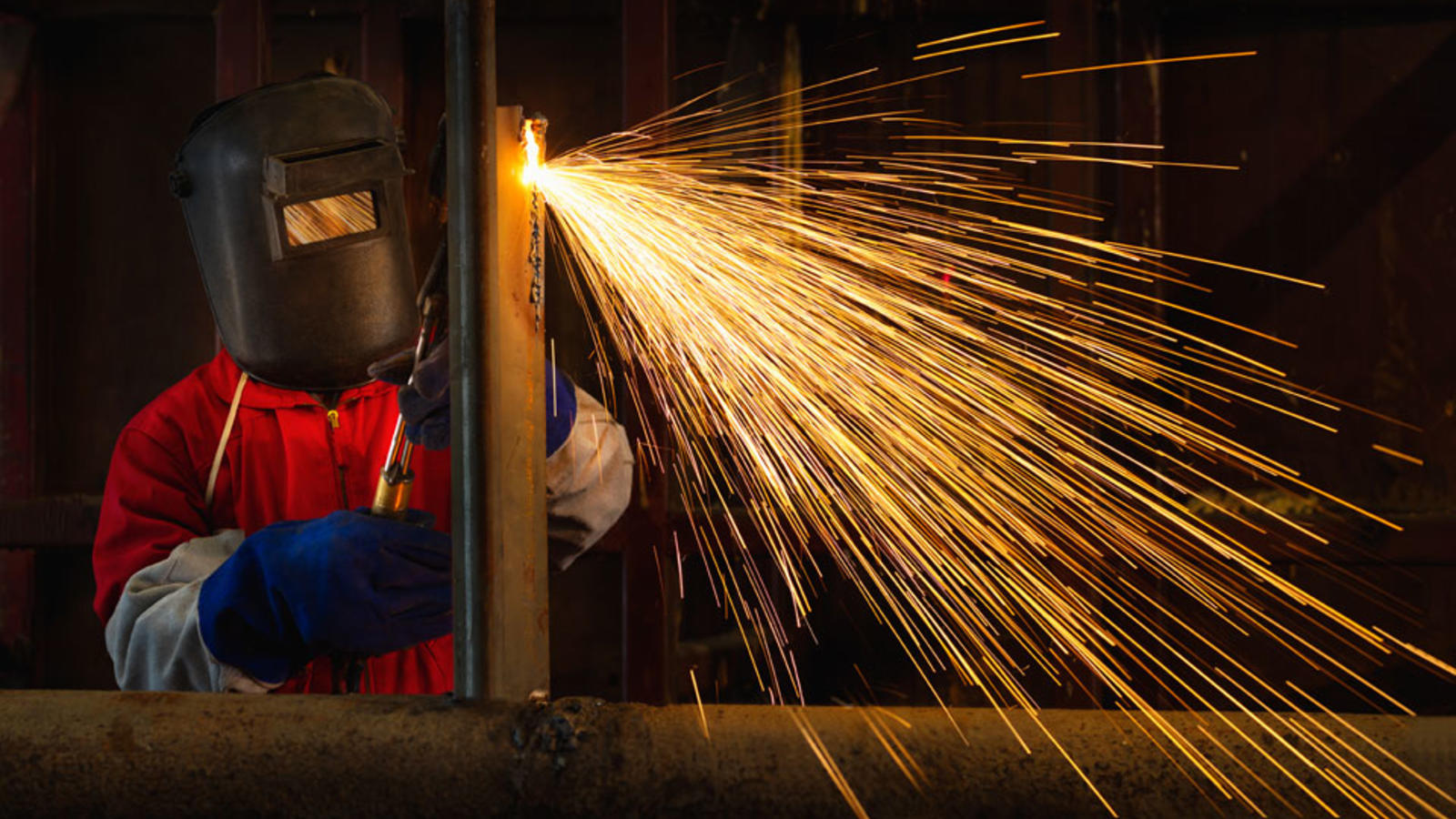
Secret Elements of WPS
Talking about the integral elements of a welding treatment specification (WPS) is necessary for understanding its function in welding procedures. One essential element of a WPS is the welding process requirements, which details the certain welding processes to be utilized, such as gas tungsten arc welding (GTAW) or shielded steel arc welding (SMAW) By integrating these vital aspects into the WPS, welding procedures can be standardized, making sure top quality, efficiency, and safety and security in welding operations.
Strategies for WPS Optimization
:max_bytes(150000):strip_icc()/MIG20welding20arc20in20action-2000-e8844d72f5094d408b5ab6f1c9436a4f.jpg)
Secondly, training and credentials of welding employees according to the specific demands of the WPS is vital. Offering comprehensive training programs and making certain that welders are licensed to perform treatments outlined in the WPS can cause higher top quality welds and minimized rework.
Furthermore, leveraging innovation such as welding software application and surveillance systems can assist in maximizing WPS. These tools can assist in monitoring variables, making certain parameters are within defined restrictions, and supplying real-time responses to welders, allowing them to make prompt changes for enhanced weld top quality.
Typical Challenges and Solutions
Facing challenges in implementing the strategies for WPS optimization can hinder welding operations' effectiveness and quality. One common challenge is inadequate training or understanding of the welding treatment specs (WPS) amongst the welding team.
Another difficulty is the lack of correct documents and record-keeping, which is essential for WPS optimization. Without clear records of welding specifications, products made use of, and evaluation results, it becomes challenging to determine locations for improvement and ensure consistency in welding processes. Applying a durable paperwork system, such as digital welding management software program, can help streamline record-keeping and help with information analysis for constant renovation.
In addition, inconsistent welding tools calibration and upkeep can position a substantial obstacle to WPS optimization. Regular equipment checks, calibration, and upkeep routines should be stuck to purely to ensure that welding parameters are properly controlled and preserved within the specified tolerances (welding WPS). her response By dealing with these usual difficulties with proactive options, welding operations can enhance efficiency, top quality, and overall welding excellence
Ideal Practices for WPS Execution
To make certain successful WPS implementation in welding operations, adherence to industry standards and meticulous focus to detail are vital. When starting WPS application, it is crucial to begin by thoroughly understanding the particular welding requirements of the job. This entails a thorough review of the welding treatment specifications, products to be bonded, and the environmental problems in which the welding will occur.
When the requirements are clear, the next step is to select the appropriate welding procedure that aligns with these specs. This involves consulting the relevant codes and criteria, such as those provided by the American Welding Culture (AWS) or the International Organization for Standardization (ISO), to make certain compliance and top quality.
Moreover, documenting the entire WPS application procedure is vital for traceability and top quality control. In-depth documents ought to be maintained concerning welding parameters, material preparation, preheat and interpass temperatures, welding consumables utilized, and any deviations from the initial treatment. Regular audits and evaluations of the WPS can aid recognize areas for enhancement and ensure recurring optimization of the welding about his process.
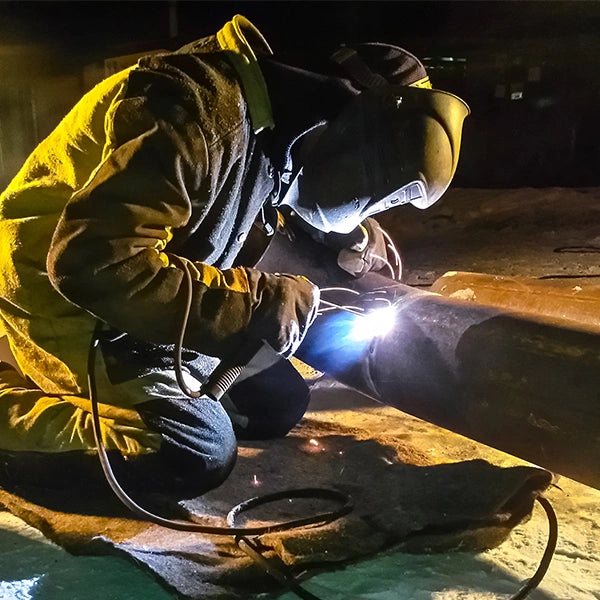

Final Thought
Finally, the execution and optimization of Welding Procedure Requirements (WPS) is critical for achieving welding excellence. By comprehending the essential elements of check here WPS, applying efficient strategies for optimization, resolving usual difficulties, and adhering to ideal methods, welders can make certain premium welds and risk-free working problems. It is crucial for experts in the welding industry to prioritize the appropriate implementation of WPS to enhance total welding efficiency and accomplish preferred outcomes.
The Importance of Welding Procedure Requirements (WPS) in the welding sector can not be overstated, offering as the foundation for ensuring uniformity, top quality, and safety and security in welding procedures. A WPS supplies detailed guidelines on just how welding is to be lugged out, consisting of necessary variables such as products, welding processes, joint layout, filler metals, preheat and interpass temperature levels, welding currents, voltages, traveling speeds, and extra. One crucial facet of a WPS is the welding process requirements, which lays out the details welding procedures to be used, such as gas tungsten arc welding (GTAW) or secured metal arc welding (SMAW) By integrating these crucial aspects into the WPS, welding procedures can be standardized, ensuring quality, performance, and security in welding procedures.
It is imperative for specialists in the welding industry to focus on the correct execution of WPS to boost general welding performance and achieve wanted outcomes.
Report this page